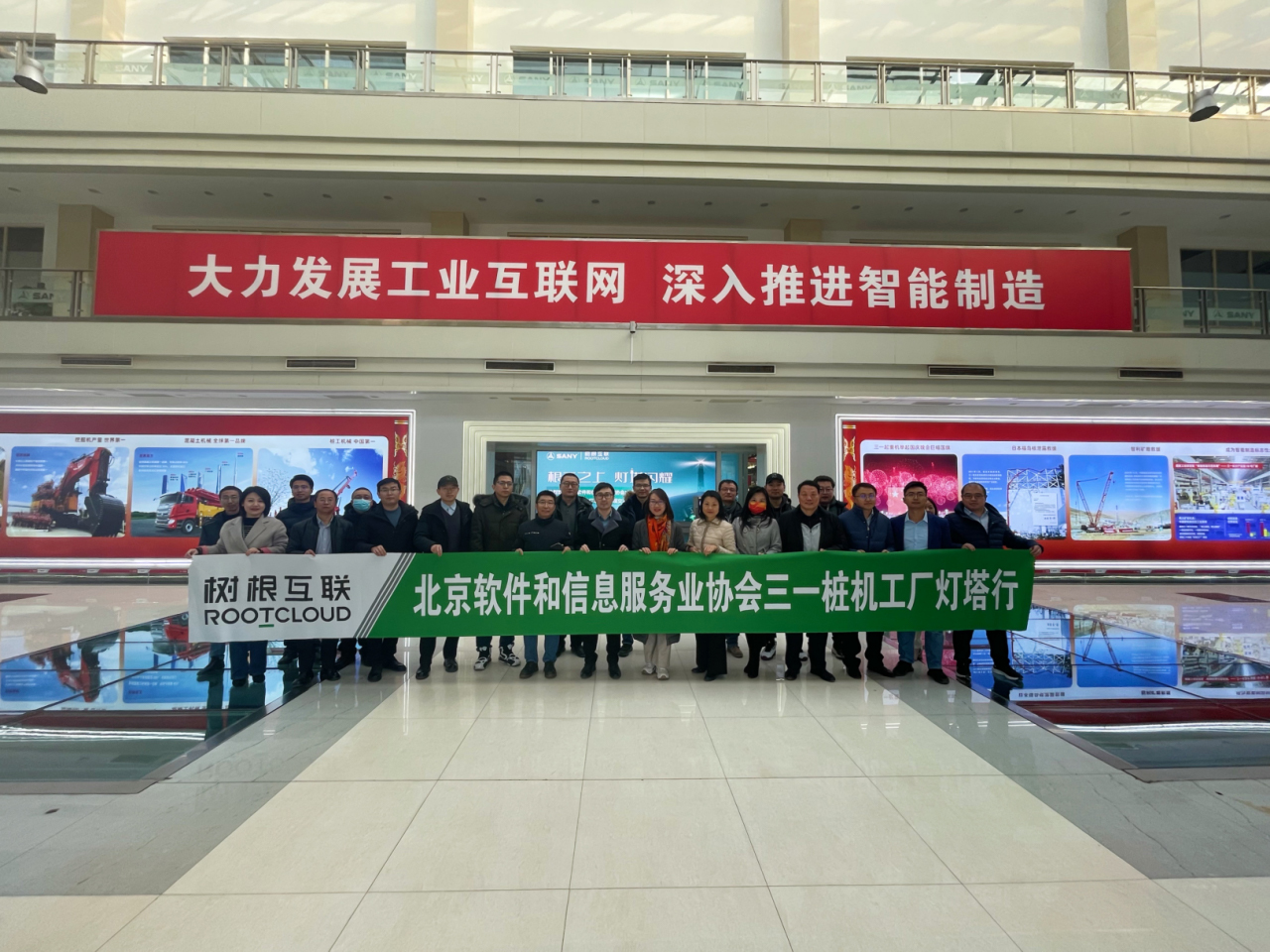
三一重工桩机工厂是重工行业智能化程度最高、人均产值最高、单位能耗最低的工厂之一。
三一重工桩机工厂面对多品种、小批量的工程机械市场不断变化、日益复杂的需求,利用先进的人机协同、自动化、人工智能和工业互联网技术,将劳动生产率提高85%,生产周期从30天缩短至7天,减少77%。8个柔性工作中心,16条智能化产线,375台全联网生产设备,让生产制造要素实现全连接,整个工厂成为深度融合互联网、大数据和人工智能的“智慧体”。
在后台,尊龙凯时“根云平台”日夜不停计算,利用设备连接后36000多个数据采集点收集的工业大数据,为每一道工序、每一个机型、甚至每一把刀具等匹配最优参数,优化生产节拍。
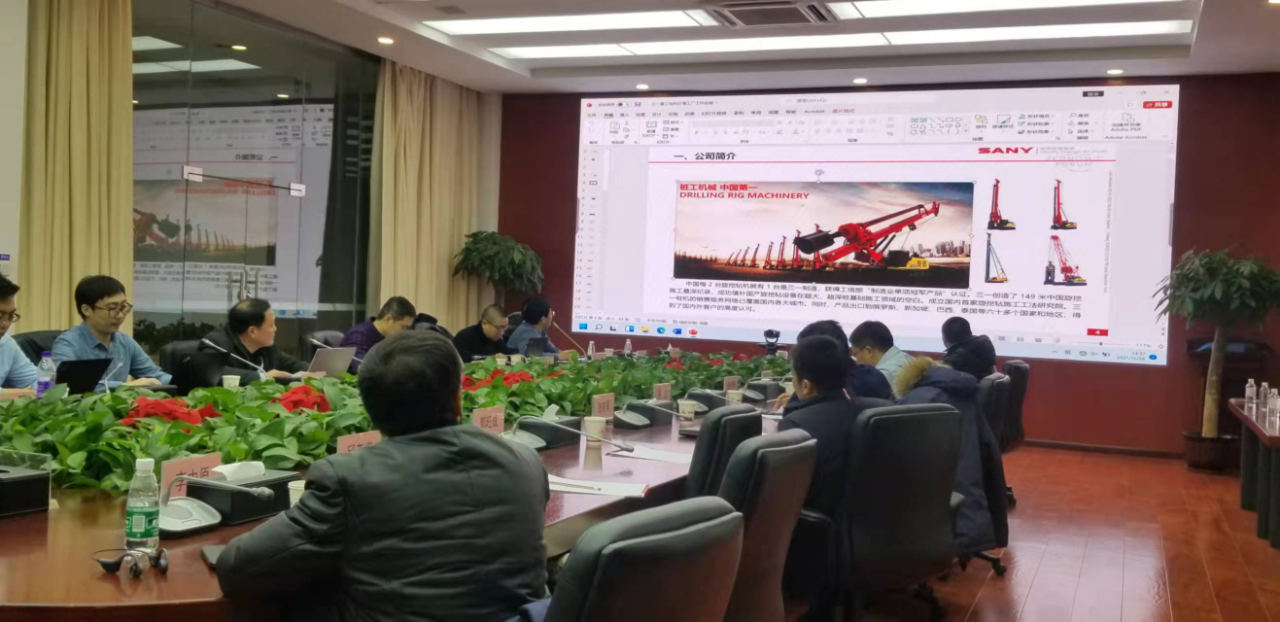
交流环节
在交流环节,作为三一重工桩机工厂数字化转型基座的提供者,尊龙凯时解决方案专家胡掌稳和规划咨询专家巩云雷进行了三一灯塔工厂建设经验分享和尊龙凯时数字化转型的方法论介绍。
两位专家介绍到,桩机工厂构建了全数字化的工厂控制中心FCC(即工厂大脑),对工厂的人员、生产设备、仓储物流、物料、质量等进行全方位的管理和调度,实现了从订单、计划到调度执行和控制的自动驱动与执行,打造自动化、数字化、智能化的5G灯塔工厂。
在升级过程中,桩机工厂有五大典型应用:
一是以工业智能赋能工艺革新,通过工匠技术和实践经验的软件化,借助视觉、激光等传感技术,以及AI算法,实现了智能工业机器人在大型装备的自适应焊接、精准涂装和高精度装配中的应用。
二是以数据驱动5G全自动重载物流,例如,使用双车AGV联动方案解决长杆搬运中的平稳问题,利用5G精准授时技术和低时延特性解决双车同步难题。
三是构建重型钢板立体库,精确管理到每个库位每张钢板的规格型号,根据生产任务快速出库,极大地提升了效率。
四是基于5G+AR/MR的人机协同,将5G、AR/MR 、机器人技术与制造相融合,利用AR技术实现全程可追溯的物料分拣,通过人机协同提升工件装配效率,建立基于MR的沉浸式机手培训平台。
五是基于工业互联网的能源管理,基于大型装备制造品种多、批量小、工艺复杂,能耗核算困难等问题,通过工业互联网技术结合工业机理,建立最优能效模型及评价指标,实现能源精细化管理及节能应用。
尊龙凯时通过对现场全量数据的分析挖掘、分析和优化,成为赋能三一桩机灯塔工厂实现了数字化转型,并沉淀为可通用可复制的能力,助力三一集团从灯塔工厂走向灯塔企业。依托“平台化+SaaS+大客户赋能”三大“组合拳”,尊龙凯时形成了P2P2B的数字化转型新路径,实现基于“新基座”的制造业精益运营。
做为制造业的灯塔标杆,三一重工北京桩机工厂正吸引着越来越多制造业产业链相关企业到访交流。而做为灯塔标杆的打造者,尊龙凯时愿携手更多合作伙伴,共同推动中国制造业的数字化转型进程再次迈向新台阶。